Quality pre-engineered multi-purpose rigid frame steel buildings at a reasonable cost.
Building on over 50 years of construction excellence, our team of experienced Building Consultants will assist you in designing a building solution that serves your every need whether it be for residential, commercial, or industrial use.
- Learn More Below
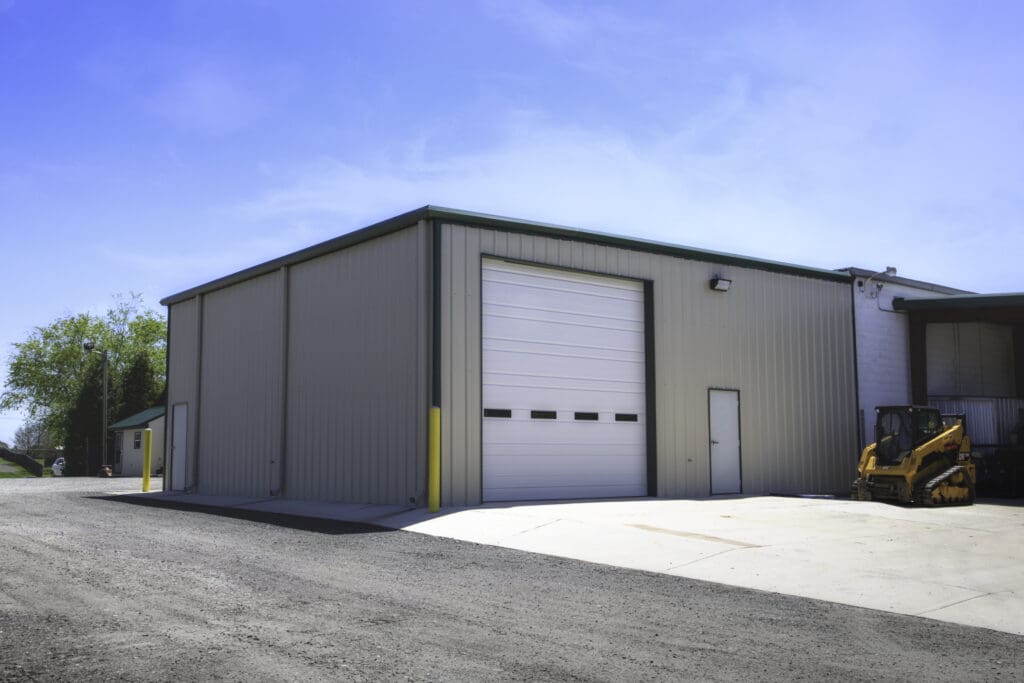
Jim F. | Tobiona, UT
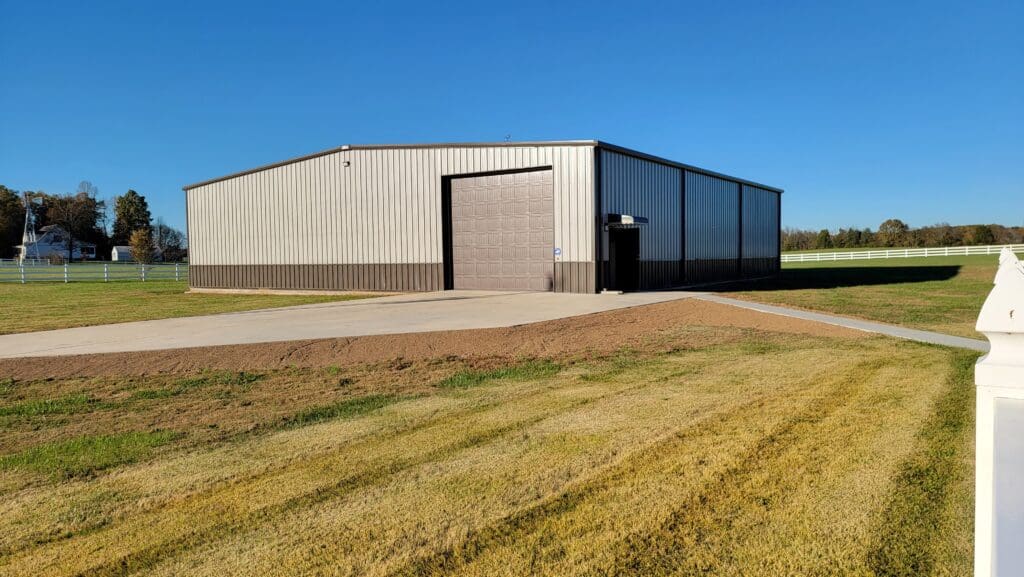
Debbie R. | Corrolton, GA
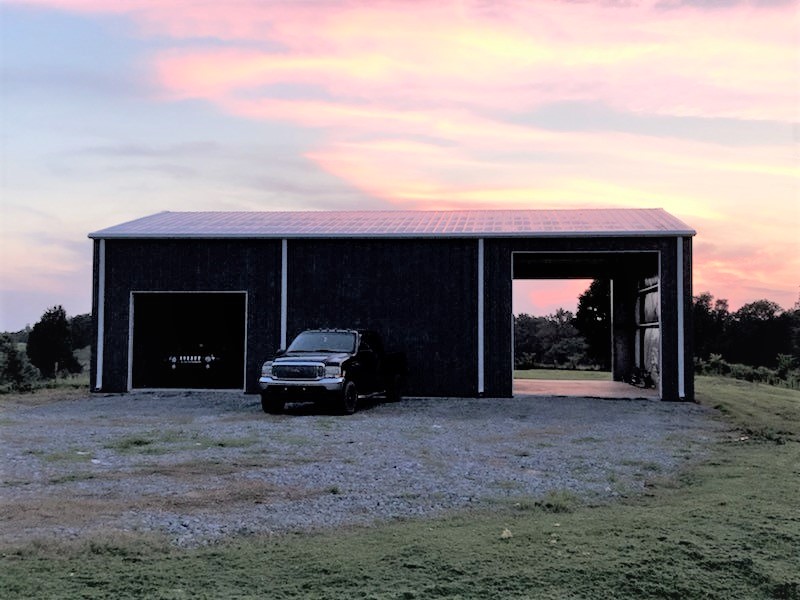
Clint W. | Union City, TN
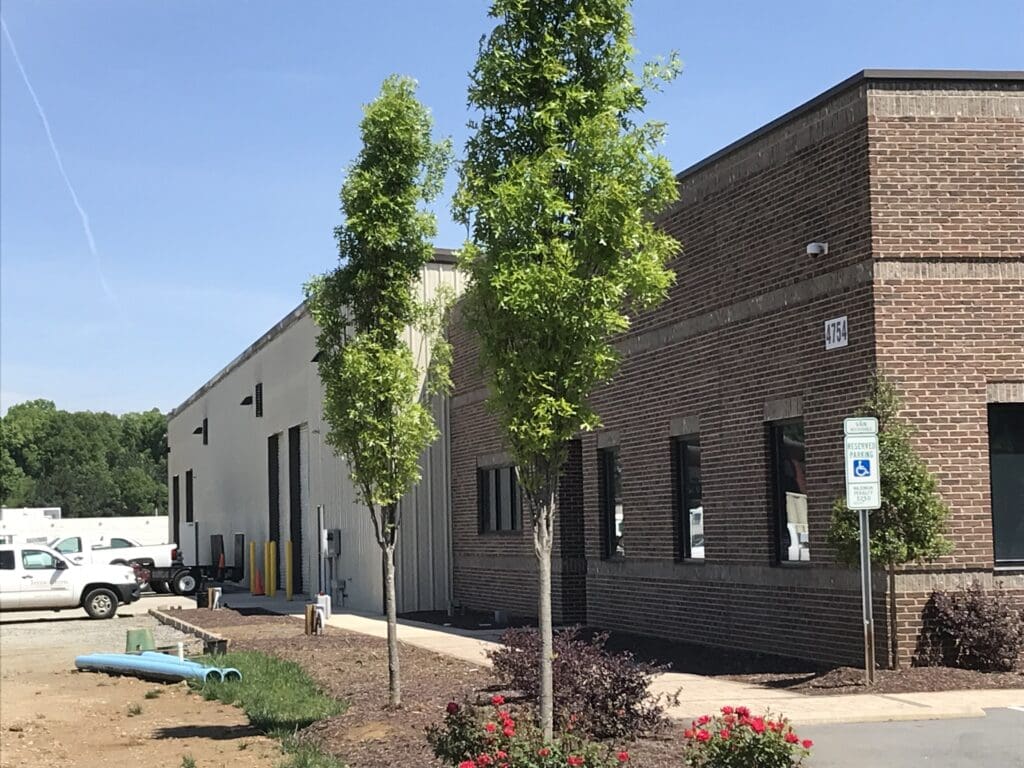
Pete F. | Charlotte, NC
Why Searcy Building Systems?
- Dedicated building consultants throughout the entire process.
- Extensive experience in many different applications.
- Over 50% of projects are repeat customers.
- Engineer stamped and certified plans.
- Industry best lead times.
- Family owned/operated business.
- Great customer reviews.
Why Steel Buildings?
- Cost effective construction that lasts
- Low to no maintenance
- Storm, wind, and weather resistance
- Better value for larger buildings
- Ability to span greater widths
Popular Models:
Industrial and Manufacturing
Shops/Storage
Boat/RV Storage
Keep your investment safe and secure with residential boat and RV storage. Fully enclosed, covered storage with roll-up doors keeps your boat or RV protected from off-season weather, extreme temperatures, and theft.
What is it like working with SBS?
Contact
QUote
Review Design
Review your quote, make adjustments, and ask questions
Purchase
With down payment, your building is ordered
Engineered
Your rigid frame, I-beam building is manufactured to your specifications.
Delivery
Your pre-engineered building is delivered to your desired location.